At the bar with Deity
Ben Morrison got in touch with Deity owner Eric Davies while compiling the Bar to Bar feature inside Issue #169.
In Issue #169 Ben Morrison lined up 8 sets of trail handlebars and their matching stems, searching for an answer on what the best choice was. He spoke to riders around the world to find out about their cockpit setup, from bar width, to rise, to stem length, and material choice and clamp diameter.
Ben also got in touch with Deity owner Eric Davies, as while most brands have jumped into making 35mm clamp bars and stems – Deity haven't found the need outside of their downhill bars. Ben was keen to find out more about their design, manufacturing and testing process.
BM: So where does Deity start when making a product to stand out from the crowd?
"Great question! In fact, there’s a tonne that goes into making solid products that stand out from the rest. For us it all starts with rider feedback and our fundamental focus on strength, function and attention to detail. When Deity began we committed 100% to create products that improved a rider’s experience rather than chasing industry trends and the never ending new standards created to release new products.
"At the heart of Deity is the rider, so we’ve positioned ourselves with the independence to listen and react to their needs without having to answer to investors, massive OEM accounts or anyone else for that matter. Our focus is specifically on your 5 points of contact on any mountain bike: handlebars, stems, grips, seats and pedals.
BM: So with a handlebar – how do you guys go about making yours different?
ED: "We believe it starts from the ground up, which is why we use the best materials available and have developed our own butting technology that is proprietary to Deity. Our Gradient Butting Technology is not just double or triple butting, it allows us the ability to put material where we want it and remove it where we can save weight regardless of the area of the bar or “butted” thickness. This allows us to produce light weight bars that are significantly stronger than competing bars at the same weight that simply use double or triple butting. In addition this allows us to control the amount of flex or damping properties in each bar without exhausting you with an over built rigid feel.
"Next we focus on the heat treatment process. Everyone heat treats aluminum handlebars, or should be, but why? We’ve found that correctly heat treating a handlebar increases its strength by 20%. However, each rise, width, bend, sweep and material has its’ own temperature and time for proper heat treating so every different model and rise needs to be heat treated separately to maximise its’ benefits. Most of our competitors do not take the additional time to heat treat each model and rise individually so they put multiple different bars, materials, and rises together in one treatment at the same temp for the same time frame, which does not properly heat treat the individual bars – resulting in less than optimal results and strength for all of their bars.
BM: What sort of testing goes on with bar designs?
ED: "When we are designing a new handlebar, it will go through these Gradient Butting and heat treatment processes before it begins our rigorous Deity proprietary in-house testing procedures. Our testing requirements are much higher than industry standards and we’ve also developed our own testing procedures to mirror what a handlebar actually goes through on the trail under a rider. Industry requires Impact and Stress Cycle testing but does not specify how this is done, so most simply use an up and down force which is never what a handlebar goes through in the real world. The angle of deflection and forces that a rider puts on a handlebar varies in different riding scenarios, and so does our testing. Once this “new” handlebar passes all these tests we will real world test for at least 12 to 24 months to make sure it is on another level of strength and performance. For example, our new BF800 Brendog – Brendan Fairclough’s Signature Handlebar launched in June has been ridden by Brendan for the past 2 World Cup seasons with the Blacklabel graphics to keep it top secret.
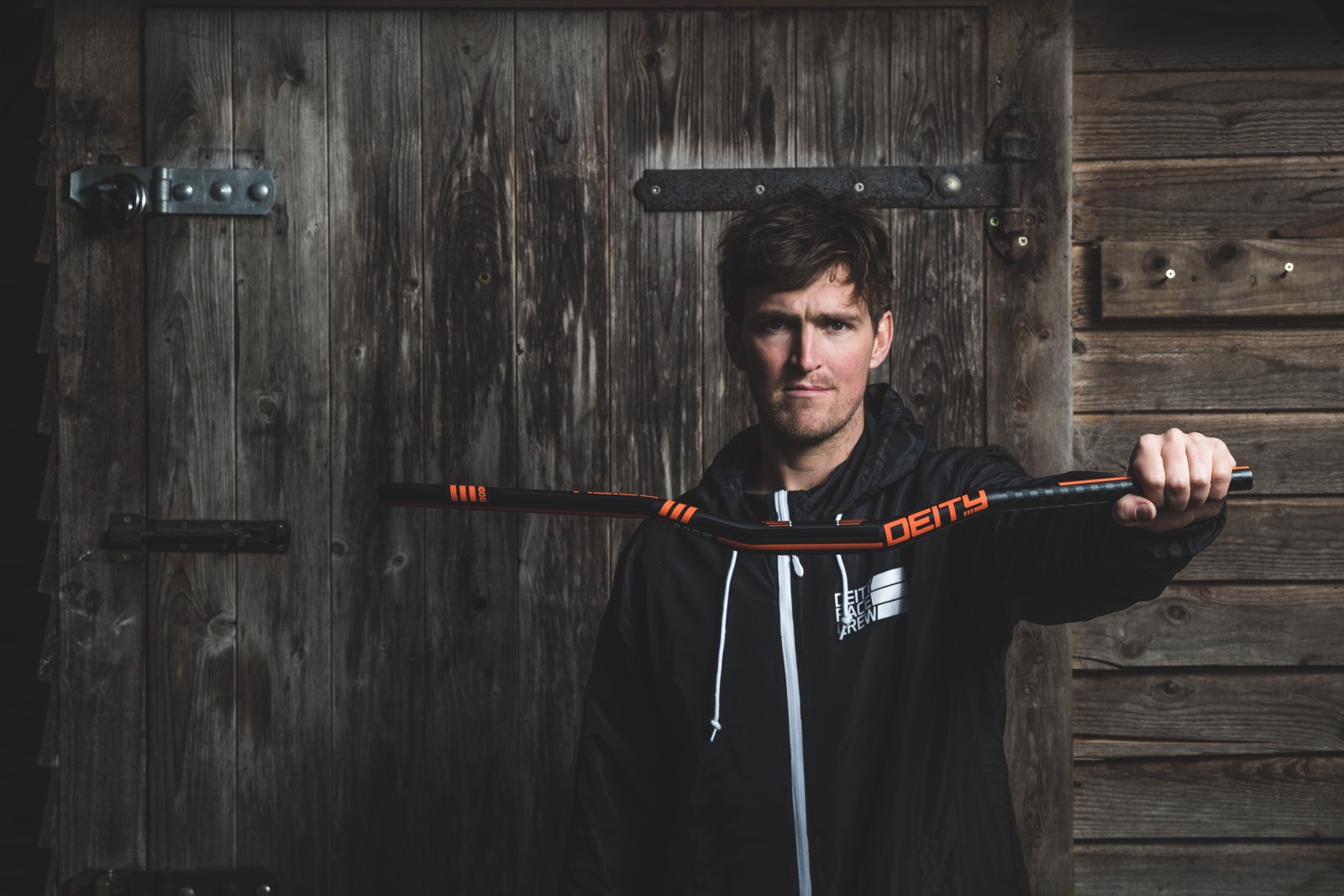
"We back all our products up with crash replacement policies to keep riders on the bike even when they are progressing and pushing their limits. Rest assured we put this level of product design, development and testing into all our products before they ever see the end rider.
BM: How close do you work with their riders and what influence do they have on products that are not just signature ones?
ED: "We test products with many of our pro riders… In addition, we seek customers who put products through the toughest conditions to test for us and attempt to destroy our new designs. Currently we are testing with our pros, a number of customers and non-Deity riders to develop new pedal technology that is yet to be utilised in cycling.
"We track the testing results and take all the feedback and experiences to heart when developing products. For example, our TMAC pedal went through many prototypes before we got it right but we refused to settle and neither did Tyler McCaul himself.
BM: "With everybody being different how do Deity settle on the up and back sweep their bars have?"
ED: "I struggled early on with wrist issues – until I had the opportunity to create my own. Back then bars were narrow with minimal rise and little up or back sweep. With the opportunity to make any version possible I settled on a 9 degree backsweep with a 5 degree upsweep because it completely alleviated all wrist and hand issues by aligning your elbows and hands in more of an ergo position. This protects your wrists and lessens the fatigue allowing riders more time on the bike.
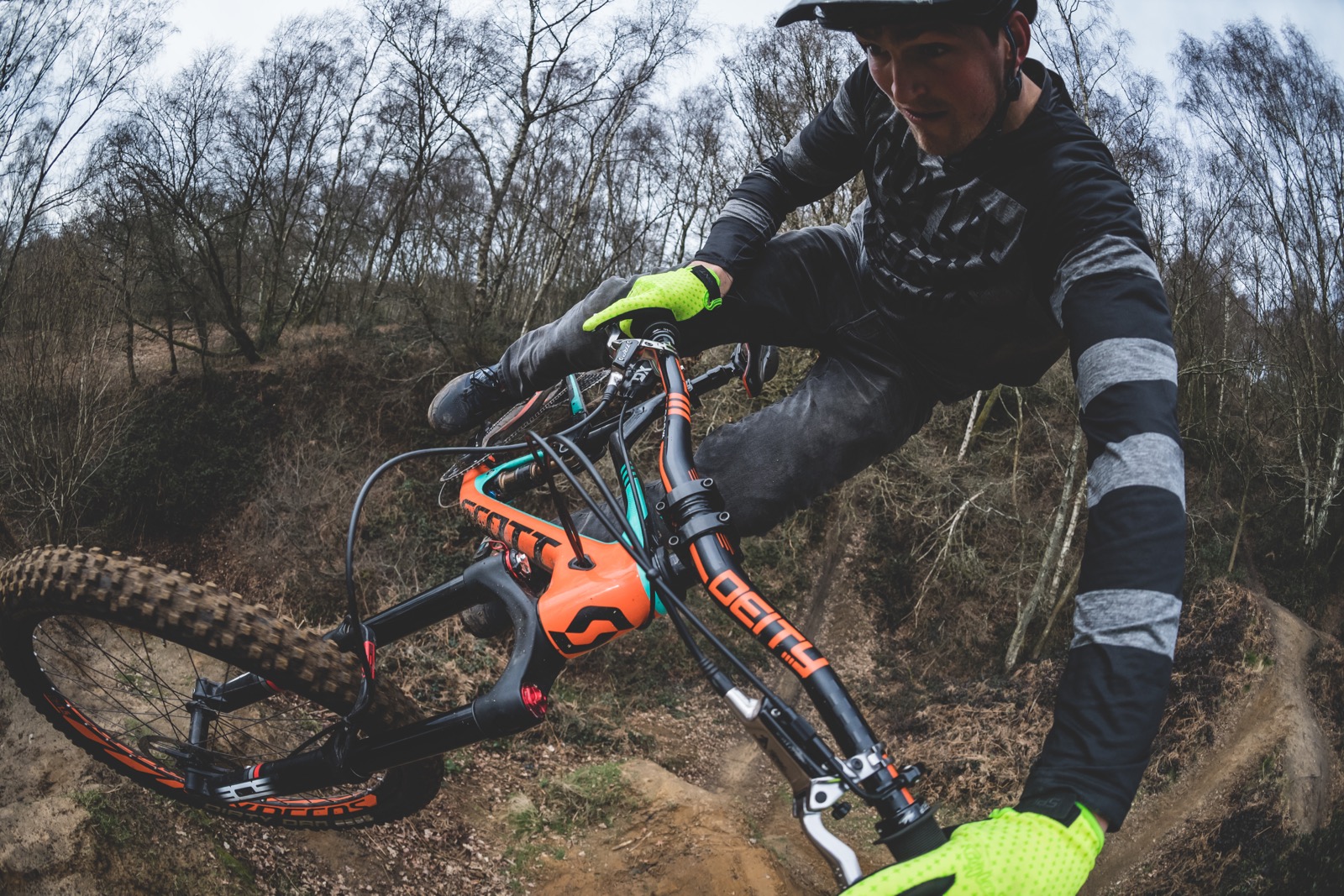
"We’ve stuck with 9 by 5 for over a decade but are expanding into other options as we develop signature products and explore new platforms like our Brendog BF800 bar which features an 8 degree backsweep. Brendan prefers this position because he feels more aggressive to attack world class Downhill courses and who are we to argue?! We will continue to add new options for different riders once we’ve tested and feel they’re winners.
BM: With the market demanding new new new rad rad rad every week how does Deity deal with this?
"There is an interesting effect throughout society right now that is fueled by massive consumption of everything… New content, new stimulation, new experiences, etc… but we’re finding this is leaving people and us feeling unfulfilled. We ask, what is the value of anything if you move on immediately to the next best thing?
"We will always create new because we are restless and constantly looking to improve what we do, but we only put a new product to market if it serves our riders and is better than what we’ve done before. We don’t release new lines annually and we don’t believe we have to… DEITY exists because of riders’ shared experiences and the recommendations that are passed between customers. This organic growth is the foundation that has built our reputation.
BM: Is there an industry standard for load and fatigue fail rates for handlebars? If so what does Deity do in there testing to meet or exceed these standards?
ED: "Yes, there are a few industry standards which we have to meet…but they are very base level. So we also add Impact Testing which is a measured weight dropped on a handlebar repeatedly until it meets a certain minimum number of cycles. We test to the point of failure and use this test on all of the major competitor’s handlebars as well to see where we stand. An Impact Test is not a requirement, but with riders like Cam Zink on our crew…we believe in pushing our bars to their limits.
"For standardized testing, there is also a stress/fatigue test that literally pulls and pushes the ends of a handlebar that is secured at the center bore by a fixture. It is surprising how easily you can meet these standards, so we also add our own proprietary cycle tests to truly mimic the abuse our product will go through. We modified this test to mirror the angles and deflection riders actually put stress on a handlebar instead of using the traditional vertical up and down movement. This allows us to replicate, as close as possible, the real world. But, we do not stop there…our cycle testing numbers are insanely high with a broader range of deflection to truly give us an idea what we are creating.
"The early days of Deity were formed by a need for product that could take the abuse of early Slopestyle and Freeriders. Most products those days were hyper focused on lightweight and lacked the strength to support these new emerging styles of mountain biking. Since the very beginning all our products are designed to hold up to these most extreme conditions and all our riders are on the same production products we sell, not a modified version for a certain event or rider.
BM: What are the advantages of a 35mm bar over a 31.8mm, if any?
ED: "There is lots of debate over this topic and we’re still working this out for Deity… We definitely feel 31.8mm bore is optimal for most applications and almost every one of our riders prefers 31.8mm. However, bars wider than 800mm and carbon bars can definitely benefit from a larger center bore. But, 35mm cannot be lighter as promoted. When 35mm bore came on the market it was pitched as stronger and lighter but you don’t see that promoted today. So you have a heavier bar that can be stiffer and more abusive if it’s not designed properly.
"We have taken our Gradient Butting technology, years of experience, and rider preferences into account and we have some killer products coming for 2019 – keep your eyes peeled!
BM: How does Deity come up with their stock widths and do they expect riders to cut them down to suit them self or run them as is out of the box?
ED: "This can also be a tricky area to perfect… We have to create bars that are wide enough for the taller, wider reach riders but also recognise that many riders will cut them down. This certainly creates a challenging paradox because the damping properties and ride quality for a specific bar is designed around the full width. So if you cut them down you no longer have the same amount of leverage which minimizes the amount of flex the bar needs to give. This results in a stiffer feeling bar the further you cut it down, so we aim to allow a 30mm range upon the development stage. Nevertheless, making a range of widths to accommodate all types of riders is definitely the way to go.
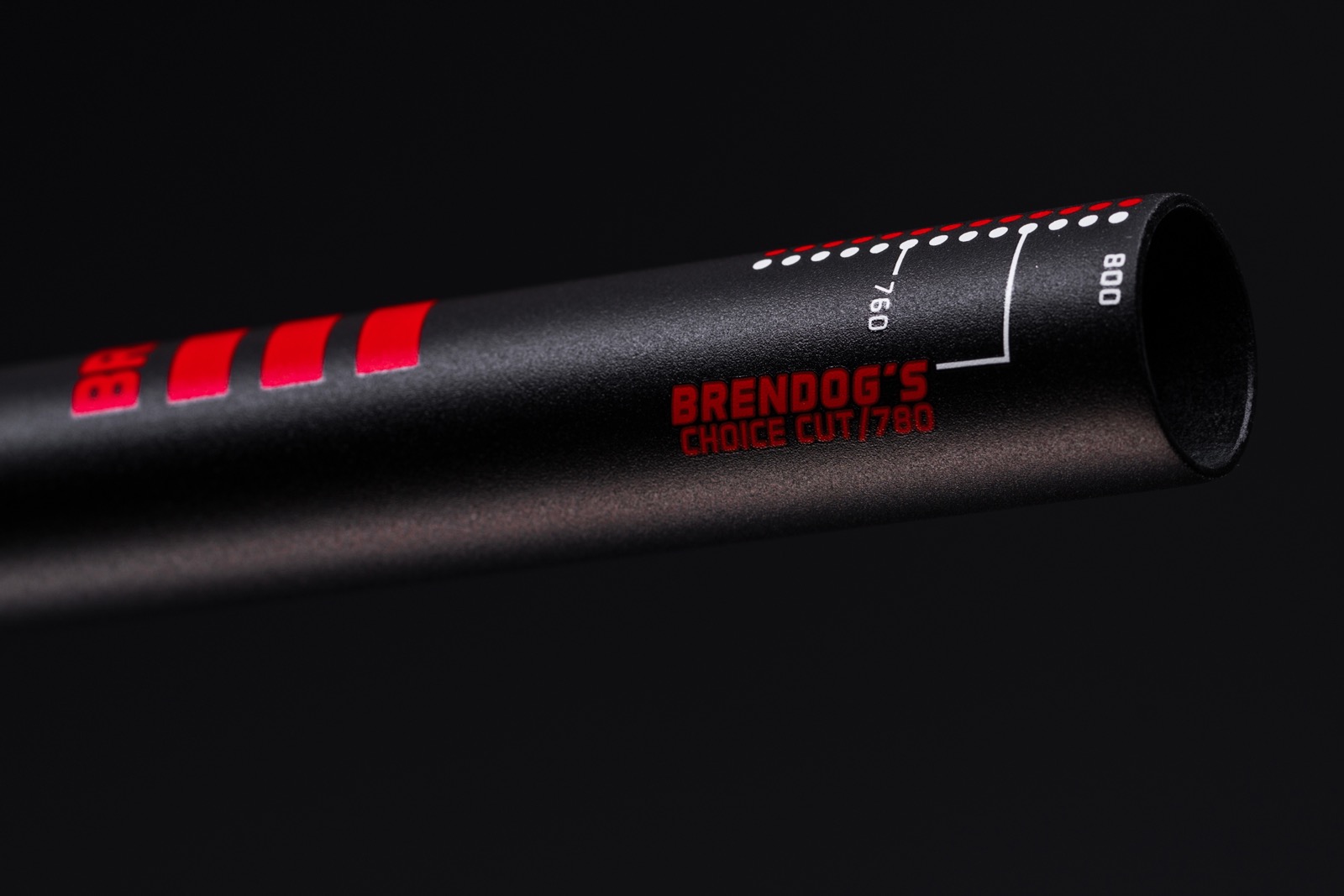
Having said that we realise people still cut bars and we recommend never cutting more than 30mm off a bar to maximsze the feeling the bar was intended to give. Regardless, we do have an upper hand in this battle because of our Gradient Butting Technology. So you will notice less increase in stiffness as you cut our bars than most other typical butted bars on the market.
"The best rule of thumb is to find a bar close to the width you are looking for and make sure to take into consideration the additional width your grips provide. Don’t forget to measure twice and cut once!
BM: Carbon over Alloy, from an manufactures standpoint what are the advantages and disadvantages?
ED: "Both aluminium and carbon have benefits and drawbacks. Carbon is an amazing material that allows you to ride a lighter bar that gives you varying flex or damping properties as compared to the same spec’d bar in aluminium. In addition, carbon is much stronger than aluminium because it has no “memory”. Carbon can flex over and over again and it never weakens the material where aluminium is weakened every time it flexes.
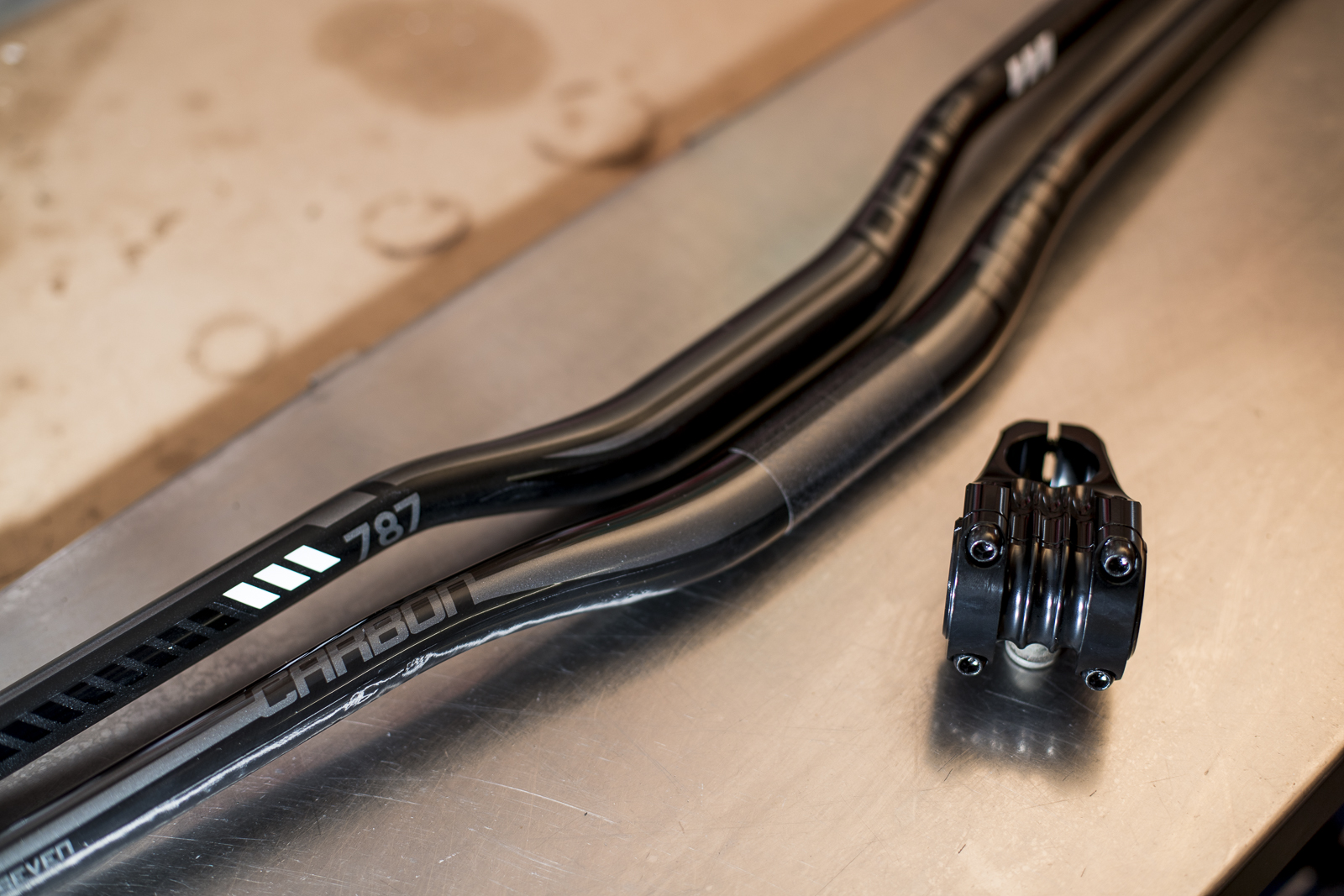
"However, the drawback of carbon is how sensitive it is to any scratches, gouges or crushing. This is why it is so critical to follow manufacturer’s torque specs on a bar (not the stem you are mounting it to) to avoid crushing the bar. You don’t see this issue nearly as much with aluminium. Also, we all know the cost for carbon is much higher than aluminium, so if you’re pushing the limits and smashing into obstacles on the trail from time to time with your bike rubber side up, carbon bars have to be replaced with any scratch, gouge or crushed area immediately and are no longer safe to ride. There is no fix for this, epoxy and other substances like this cannot fix the damage and significantly weaken the state of a carbon bar once it has any damage as we mentioned.
"This is where an aluminum bar shines… Aluminum can handle scratches and impacts much better and still be safe to ride. Our rule of thumb is to consider your budget and how aggressively you’ll be pushing your limits.
Don't miss Issue #169, where Ben puts his findings together from the 8 bars and stem setups he tested.
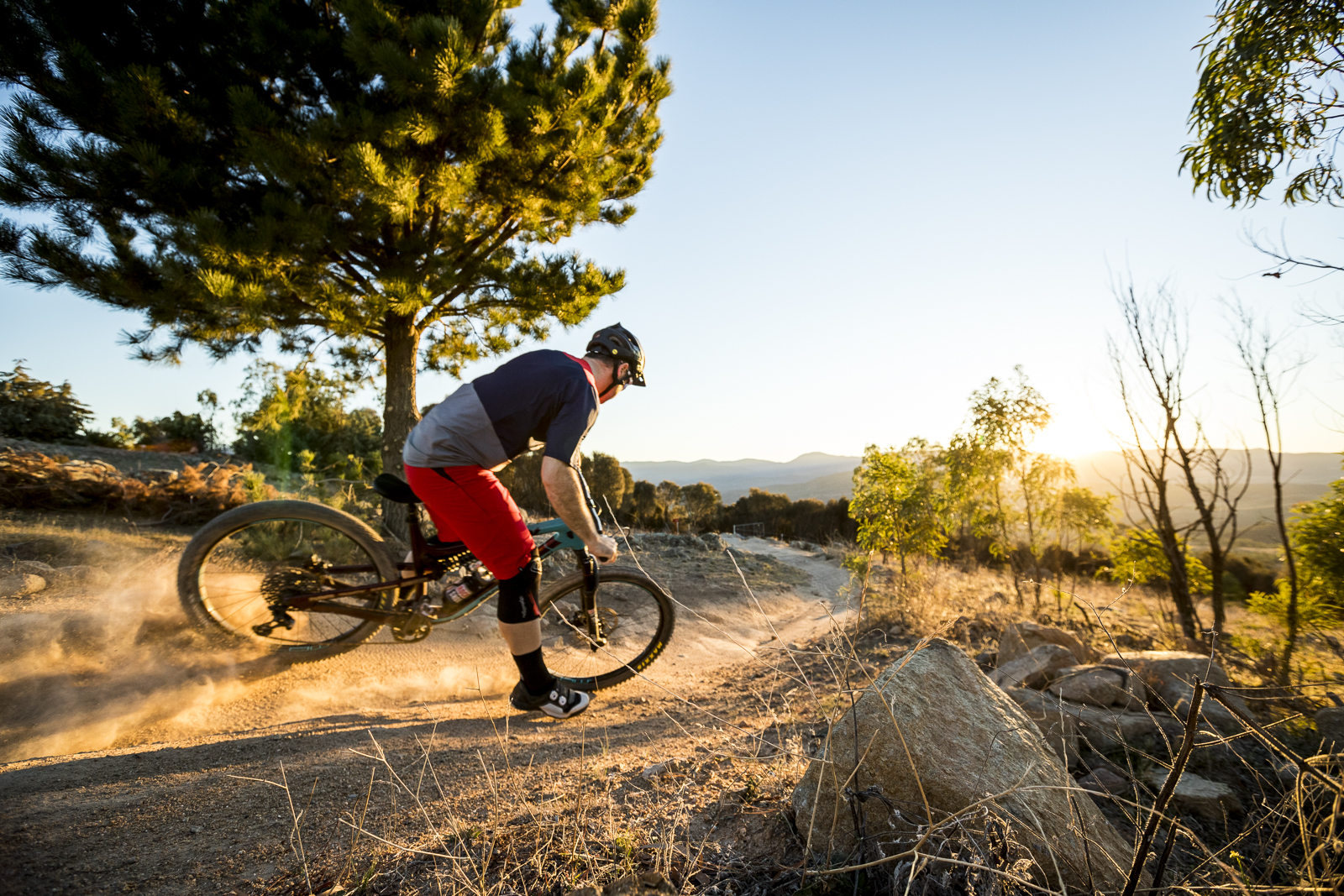