The Holy Trinity of Mountain Bike Design
Standing out among the crowd, there is one homegrown bike which bucks the trend.
Words: Hayden Wright | Photos: Nigel Petrie
On a hot summer's day in the shuttle line at Mystic Mountain Bike Park you are likely to see a laundry list of the latest and greatest gravity bikes available in Australia. Carbon fibre, high pivot, mixed wheel – name your flavour and it's certain that your cravings will be satisfied. These high end, high dollar bikes are all developed for years behind closed doors, with design secrets being kept under lock and key until the frame is deemed ready for marketing and mass consumption.
Standing out among the crowd, there is one homegrown bike which bucks this trend. Through the combination of their truly unique take on bicycle design, choice of materials, and construction ideologies, the three men behind Trinity MTB are in the process of developing a genre bending and thought-provoking mountain bike in plain daylight.
Design
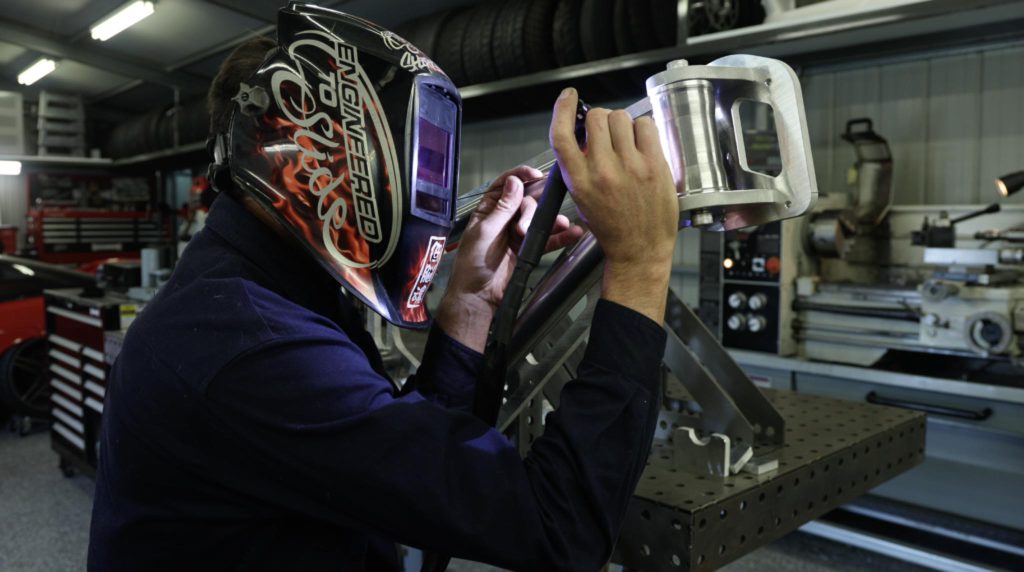
Images of Trinity’s first prototype surfaced quietly on their self-named social media page in early 2021, bringing with it all of the features required to make it an instant parable for comment sections and internet forums alike. Sleek renders of the gearbox equipped, high pivot downhill bike made entirely from billet aluminium left many salivating. The project was brought to life in partnership between Chase Warner (Designer), Mic Williams (Engineer) and Nigel Petrie (Fabricator), a global trinity who share their culture of innovation across an Instagram group chat rather than a boardroom table. This first taste of Trinity MTB had begun a steady current of curiosity online. Anticipation was widespread for a rolling prototype, with keen followers looking forward to the promised debut at the 2021 Handmade Bicycle Show.
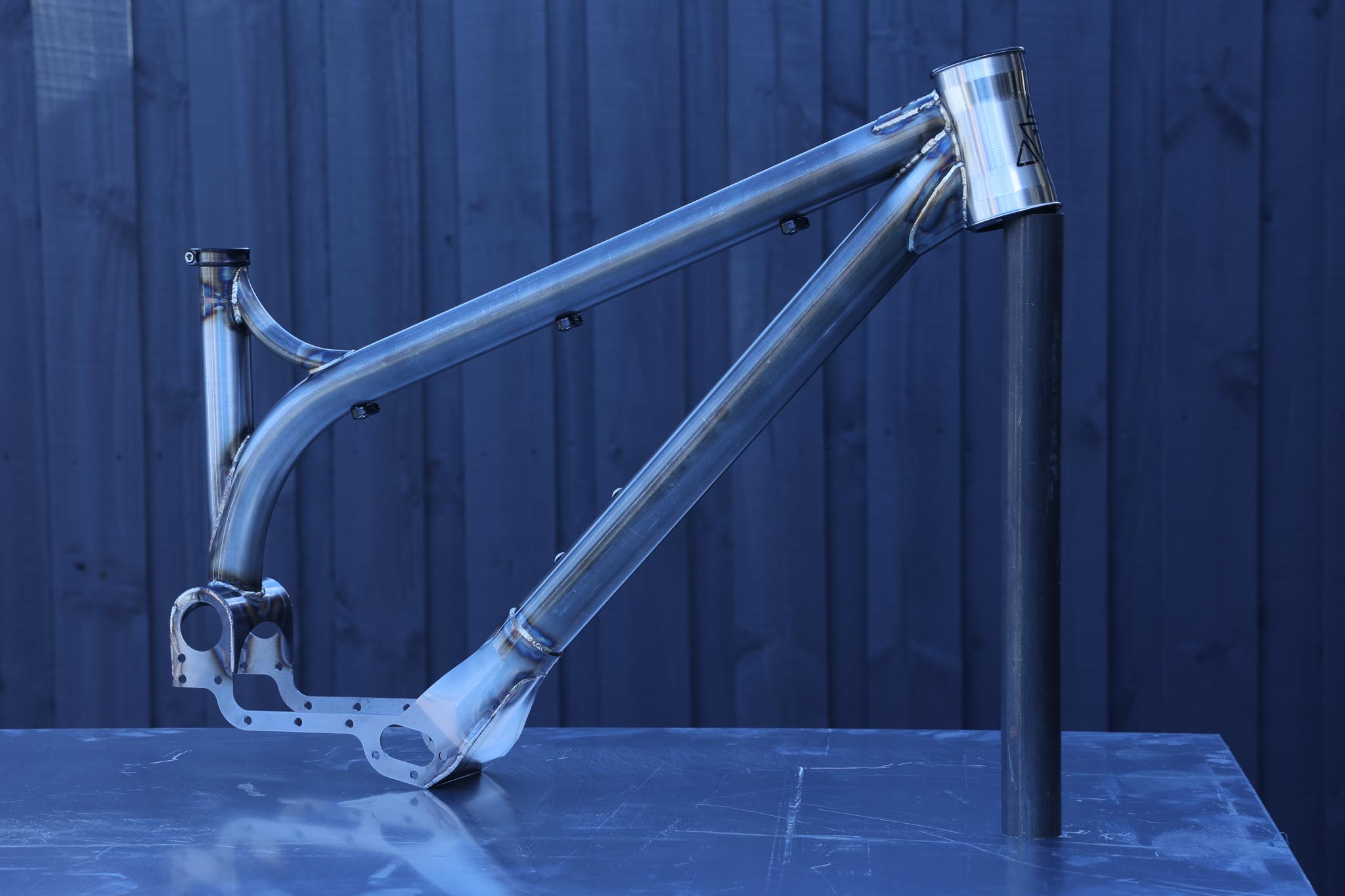
While the billet front triangle was soon abandoned for a list of reasons, namely cost and availability, the rest of the features made their way from CAD to reality. Pictures of the prototype V1 caught the eye of many, with particular praise being given to the unashamed beauty of the polished chromoly steel front end. However, when delving into the details, it was the bike’s modularity which really set it apart. The frame design accommodated the provision for either traditional or gearbox drivetrains, with the removable bottom bracket assembly being the self-proclaimed ‘heart’ of the Trinity MTB project – and their true differentiator.
Through three more prototypes this unique heart has been maintained, with Mic Williams of Williams' Racing Products developing his own gearbox to suit. In true Trinity MTB fashion this has had full transparency via his social media pages, showing the trials and tribulations of trying to reinvent the wheel. While some companies claim their bike to be a quiver killer in factory form, the Trinity is quite the opposite with customisation and adaptability at the core of their design ethos. This has also seen features such as a 56mm head tube and mixed wheel compatibility thrown into the fray, along with two separate rear travel options for DH and Enduro (200/175mm respectively). There are hints to future developments such as modular seat post masts and E motor compatibility, although don’t expect to see any of this in their first production run. Prototyping, research and development is most certainly an iterative process, and through this brand we the consumers are being taken along for the ride.
Materials & Construction
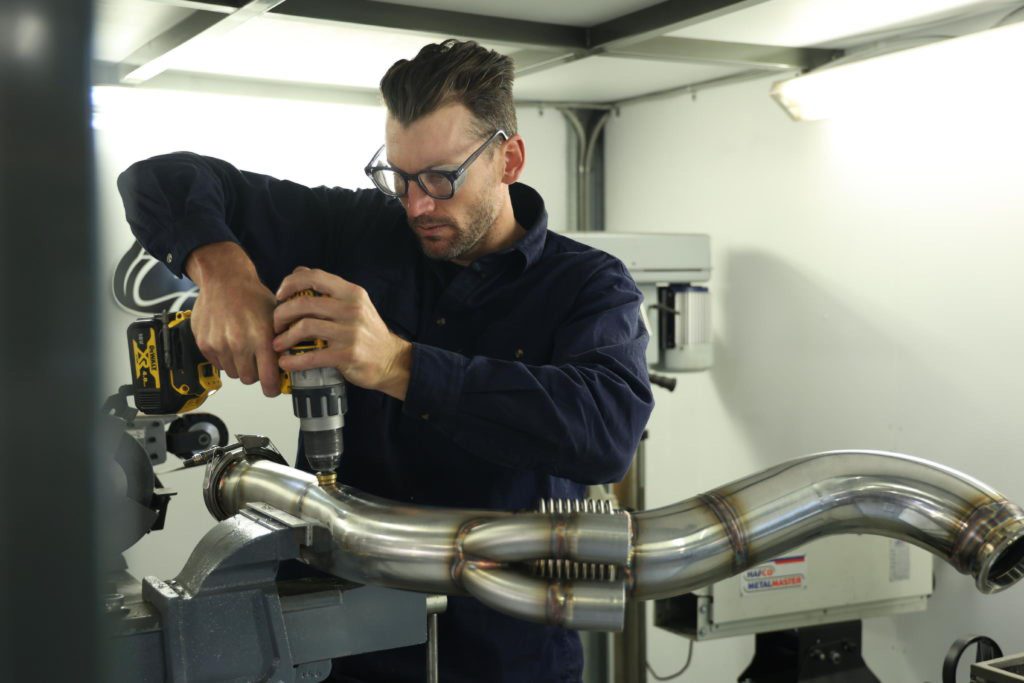
While some features on the Trinity MTB project are at the cutting edge, there are some that hark back to the roots of our sport. Primarily, their choice to use 0.9mm thick 4130 Chromoly steel for the front triangle. A material seldom seen on anything outside of aggressive hardtails and single pivot trail bikes in the mountain bike market, this particular grade and thickness of steel was deemed to be perfect for the application at hand for multiple reasons. First, it is a material that fabricator Nigel Petrie is exceptionally proficient at working with. You need to merely glance at his personal social media page @engineeredtoslide to see that Nigel is an imaginative and detail-oriented fabricator with a unique skill set that is entirely his own. Through 20+ years of fitting and fabrication experience, Nigel helps guide the Trinity MTB team from analysis to reality, ensuring that all design decisions made are feasible. All Trinity prototypes and production frames are to be made in his home workshop, so it was key to ensure that the selected front triangle material was accessible and workable for Nigel while also meeting their performance criteria.
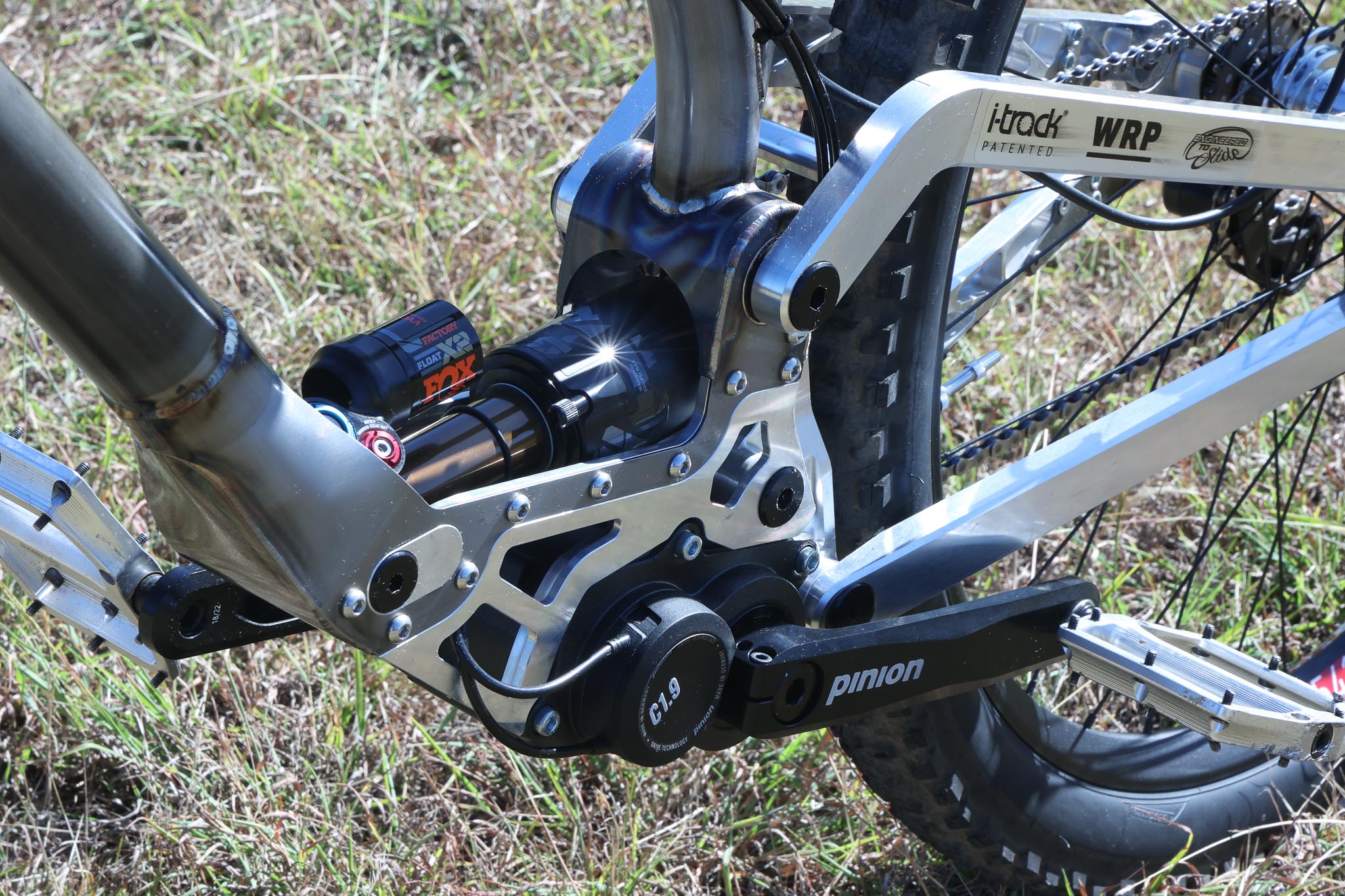
Second, Chromoly steel was chosen for its strength and resilience. Forgiving in nature when specced correctly while maintaining long term reliability, the steel front end we see in Prototype V4, with its unique swooping one piece top and down tube gives the team at Trinity the exact ride characteristics they’re looking for. Previous iterations of their frames have also featured 3D printed titanium lugs similar to an Atherton bike, but these have been cast aside due to weight concerns and a desire to ensure complete supply chain control.
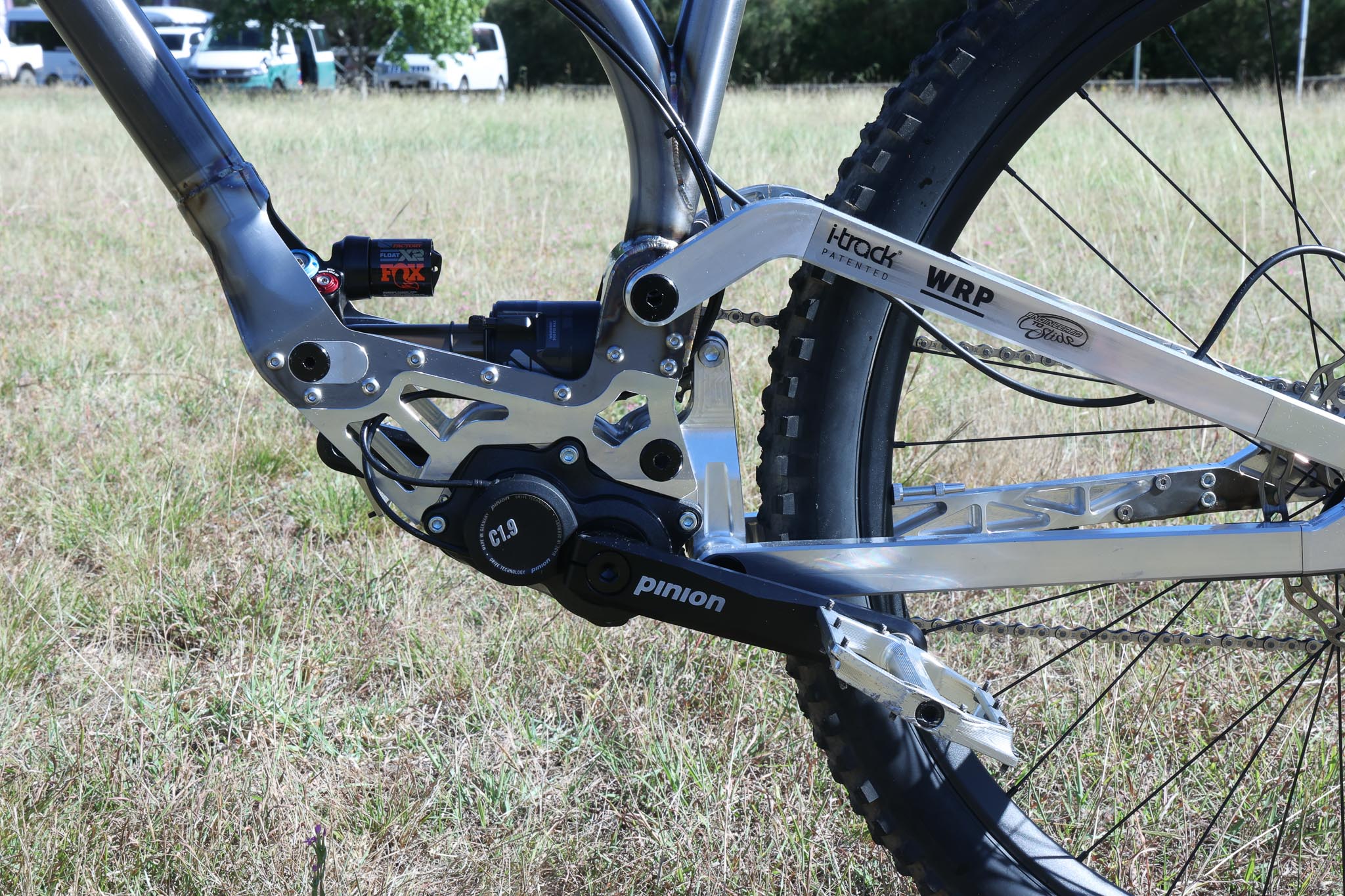
Conversely the rear end of the Trinity does away with hand crafted steelwork and instead is made from multiple 6061 billet aluminium members. A decision made to realise the same priorities as the front end through different execution, the billet construction allows Trinity to tune the stiffness and strength of the chassis to the nth degree while still keeping their supply chain local and material waste down. Billet alloy is also used for the shock linkage, which incorporates an i-Track idler-based design.
Exclusive – Riding the Trinity V4.002
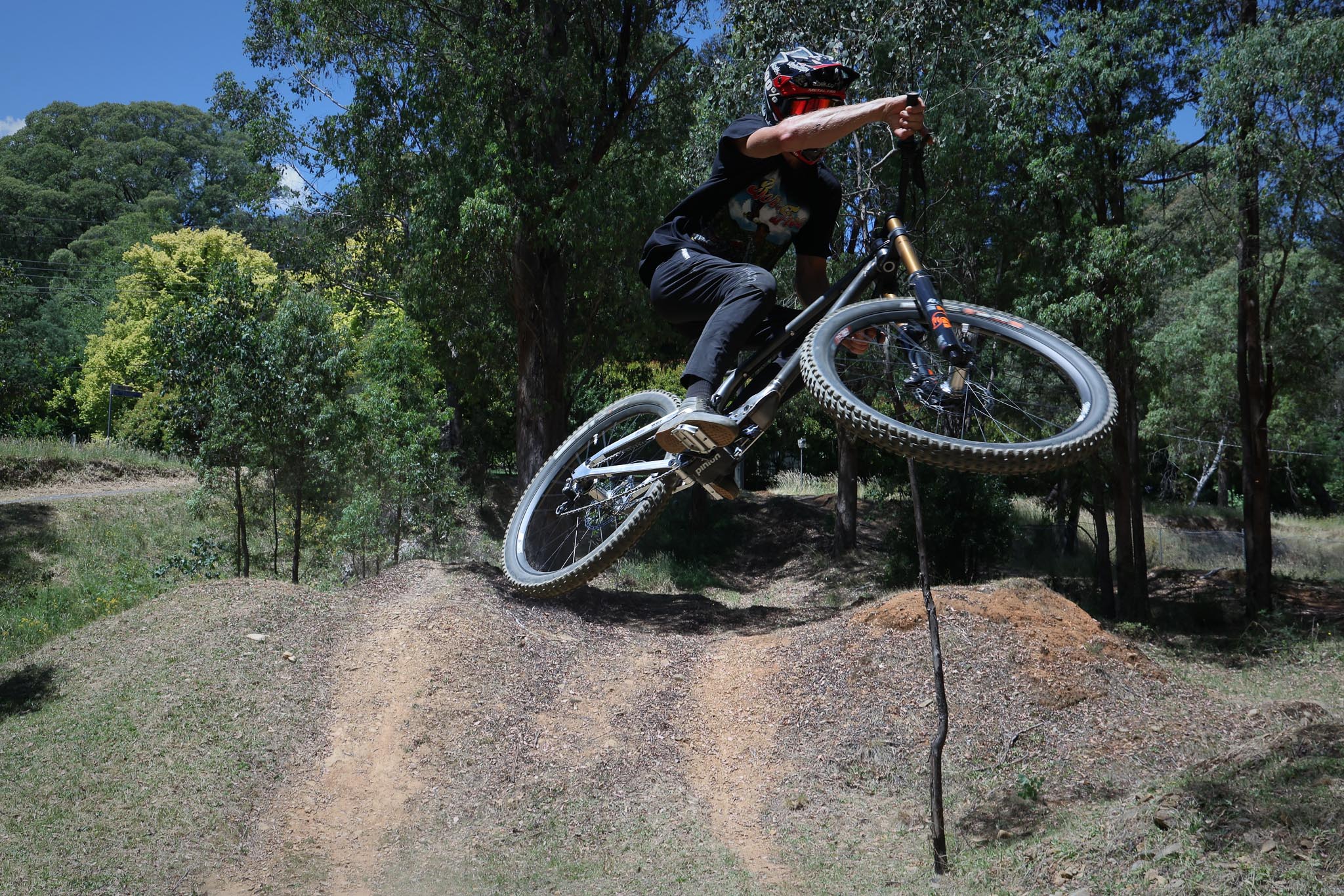
There is only one thing better than admiring a bike through your phone screen, and that is riding it for yourself. I was fortunate enough to have the opportunity to be the first mountain bike media member to pilot one of their frames, with Mystic Mountain Bike Park as the chosen proving ground. While not an exhaustive test like you would typically find in the pages of this magazine it did give me an insight into what this bike actually feels like on the trail in DH configuration and with a Pinion gearbox installed. After going through a quick basic setup process to ensure the contact points and pressures were to my liking, I headed up the hill with Nigel and went for a lap of the venerable Hero trail. That lap was quite the eye opener, as were the following 3 that I took on the handmade machine. My scrawled notes from the day listed the following ride characteristics: composed, compliant, tight – pinion?
Up first, and in my opinion most importantly, is the composure of this bike. Trinity MTB has achieved a sense of balance through the implementation of a rearward axle path and a 1:1 static front to rear centre ratio, with the bike I was riding having a 460mm reach and 460mm rear end. On the trail this made the bike very easy to control, particularly when things got steep and rough. The long rear end lends itself to putting more weight bias on the front, giving supreme traction under braking and through turns. It was through these steep rough sections, along with a few intentional overjumps that I also picked up on the compliance of the chassis. Compared to the Forbidden Dreadnought I typically ride; the Trinity had a much more deadened feel through harsh impacts. Undoubtedly this is thanks in part to the frame material choices made.
Given this bike is a working prototype I did expect there to be some chinks in the armour, particularly in the billet rear end and suspension linkage. I’ve ridden many bikes that either had or developed play throughout a day of descending, and anticipated similar from the Trinity. To my surprise, there was no noticeable play or knocking from the rear of the bike every time I grabbed the rear wheel and pushed it from side to side. Although the billet chain stays did have a makeshift tensile support, an admitted band-aid fix on this V4 mule, the bike ran without a hiccup and was also near silent. As the old saying goes, a quiet bike is a fast bike, and that rang true on this sunny morning of runs. The Trinity had no chain slap to speak of, with the only soundtrack to my riding being the dulcet tones of the suspension and tyres working to keep me on my chosen line.
I would attribute most of this silence to the Pinion gearbox, which brings with it positive traits such as the above along with an improvement to ride character and suspension action. Outside the obvious benefits of having a sealed drivetrain mounted out of harm's way, a key feature of a bottom bracket mounted gearbox is that it allows a substantial decrease in unsprung mass at the rear wheel of anywhere between 500 and 1000 grams depending on your setup. Put simply, this gives an increase in shock performance as it has less weight to control at the rear axle. This was admittedly difficult to pick up on during my test runs, as I had no regular drivetrain to compare against. I will however say that the rear suspension action on the Trinity was some of the best I have ever felt, and I have no doubt the gearbox has a heavy influence on this. The rear of the bike tracked bumps and holes effortlessly, thanks in part to the minimised unsprung forces being transmitted through the shock.
It was during pedalling that I noticed what is undoubtedly the most well documented drawback of the Pinion setup. Not being able to pedal while changing gears was a real brain melter, and would take quite some getting used to if you rode full time on a Pinion box. Riding with foresight seemed to help things, but I did miss being able to blast through the gears while sprinting out of a turn. I am without a doubt a believer that gearboxes are superior in theory to a standard mountain bike drivetrain, but I feel the Pinion is a stepping stone in the right direction rather than the ultimate solution to the problem. Fortunately, through Trinity’s implementation of the modular bottom bracket, they’re not locked into one single solution and can adapt to changes in drivetrain technology as they’re made available to us.
What’s Next
2023 Is looking to be a banner year for this start up brand, with production models now rolling out to customers. I wouldn’t be surprised to see a hand made Australian downhill bike between the tape at some UCI events in the not too distant future. Until then, I’m sure the three brains behind this operation will keep us all up to date, warts and all, via @TrinityMTB.